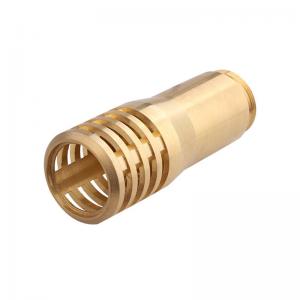
Add to Cart
CNC Turning Parts Brass Lathe Machining CNC Parts CNC Machining Services Spare Parts
CNC turning is a metal fabrication process where a part is securely held on a rotating spindle.
The spindle makes contact with a stationary cutting tool to remove material, shaping the part
to its desired form.
The primary advantage of CNC turning is its ability to create complex geometries that may
not be feasible with CNC milling.
This is particularly valuable for cylindrical parts or intricate, wavy features that would pose
challenges on a CNC mill.
However, it's important to note that CNC turning can produce various shapes beyond rounded
ones, including square and hexagonal geometries.
Product Details
CNC turning encompasses a wide range of materials, primarily categorized into three major
groups: plastics, soft metals, and hard metals.
These materials include aluminum, bronze, copper, ceramics, plywood, steel, stone, wood,
zinc, and numerous others.
The choice of material depends on ease of workability and desired properties, with those
offering favorable characteristics often being preferred in CNC turning applications.
Common Materials | |
Name | Description |
Aluminum | High machinability and ductility, good strength-to-weight ratio. |
Stainless steel | High tensile strength, corrosion and temperature resistant. |
Mild steel | High machinability and weldability, high stiffness. |
Brass | Low friction, excellent electrical conductivity, golden appearance. |
Copper | Excellent thermal and electrical conductivity. |
Titanium | Excellent strength to weight ratio, used in aerospace, automotive and medical industries. |
POM | High stiffness, high accuracy, low friction, easy to machine. |
ABS | Common thermoplastic, impact resistant, easy to machine. |
CNC Turning Tolerances | ||
Limits for nominal size | Plastics | Metals |
0.5mm* to 3mm | ±0.1mm | ±0.05mm |
Over 3mm to 6mm | ±0.1mm | ±0.05mm |
Over 6mm to 30mm | ±0.2mm | ±0.10mm |
Over 30mm to 120mm | ±0.3mm | ±0.15mm |
Over 120mm to 400mm | ±0.5mm | ±0.20mm |
Over 400mm to 1000mm | ±0.8mm | ±0.30mm |
Over 1000mm to 2000mm | ±1.2mm | ±0.50mm |
Over 2000mm to 4000mm | ±2.0mm | |
*Please clearly indicate tolerances for nominal sizes below 0.5mm on your technical drawing. |
Applications of CNC Turning Parts
Turning is employed to craft rotational components, usually axially symmetric, with diverse
characteristics like holes, grooves, threads, tapers, differing diameter levels, and even intricate
contoured surfaces.
Products wholly manufactured via turning often encompass components required in limited
quantities, notably for prototypes, such as custom-designed shafts and fasteners.
Furthermore, turning frequently serves as a secondary process for introducing or enhancing
features on parts that were initially crafted using an alternative method.
Some instances of items produced through turning encompass camshafts, crankshafts, baseball
bats, bowls, cue sticks, signboards, musical instruments, as well as table and chair legs.
Company Profile
FAQ's
1. Accuracy in CNC Turning
CNC lathes are renowned for their remarkable accuracy and precision, particularly when
machining hard materials like steel, aluminum, stainless steel, titanium, brass, and copper.
While plastic materials can also be utilized with CNC turning, their inherent properties generally
result in slightly lower achievable tolerances compared to their metal counterparts, and they
may be more susceptible to deformation during machining.
Additionally, plastic materials tend to be more cost-effective than metals, making them a favored
choice for specific applications.
Typically, CNC turning machines can maintain accuracy and repeatability within a few thousandths
of an inch.
With the right equipment and setup, CNC lathes can even achieve tolerances within a few
ten-thousandths of an inch or better. However, achieving such high precision depends on factors
such as material temperature, machine quality, and the geometry of the part being machined.
2. Advantages of the Turning Process
The turning process offers several advantages, including:
1. Versatile Material Compatibility:
Turning can be applied to a wide range of materials, including metals, wood, and plastics, making
it a highly versatile manufacturing process.
2. Exceptional Tolerance:
Turning allows for the creation of parts with exceptionally high tolerances.
Its ability to achieve precise surface finishes and tight tolerances makes it ideal for adding
precision rotational features to already formed parts.
3. Short Lead Time:
Turning is known for its short lead time, which refers to the time between order placement and
final delivery. The efficiency of the turning process contributes to its quick turnaround.
4. Minimal Operator Expertise Required:
Unlike some complex machining processes, turning does not demand a highly skilled machine
operator. A machinist can attain certification from an accredited industrial training organization
after completing a standard amount of coursework to operate a CNC lathe effectively.
5. Adjustable Material Removal Rate:
Turning offers the advantage of adjustable material removal rates. Lathes can operate at varying
speeds, allowing for precise control over material removal based on factors like the material being
machined and the desired end product.
These advantages make the turning process a valuable choice in manufacturing, offering flexibility,
precision, efficiency, and ease of operation across a broad spectrum of materials and applications.