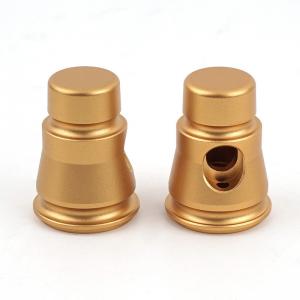
Add to Cart
CNC Machining Turning Part CNC Machining Steel Stainless Parts Small Metal Parts
CNC turning is suitable for both prototypes and large-scale production.
It offers cost-effective production for large quantities while also allowing for efficient machining
of prototypes with quick setup and programming adjustments.
Product Details
CNC turning is a versatile machining process that can effectively work with various materials.
These materials include metals like aluminum, steel, brass, and titanium, as well as plastics
such as acrylic, nylon, and polycarbonate.
Common Materials | |
Name | Description |
Aluminum | High machinability and ductility, good strength-to-weight ratio. |
Stainless steel | High tensile strength, corrosion and temperature resistant. |
Mild steel | High machinability and weldability, high stiffness. |
Brass | Low friction, excellent electrical conductivity, golden appearance. |
Copper | Excellent thermal and electrical conductivity. |
Titanium | Excellent strength to weight ratio, used in aerospace, automotive and medical industries. |
POM | High stiffness, high accuracy, low friction, easy to machine. |
ABS | Common thermoplastic, impact resistant, easy to machine. |
Nylon | Excellent mechanical properties, thermal, chemical and abrasion resistant. |
CNC Machining Tolerances
Typical machining tolerances fall within the range of ± 0.005 inches or 0.13 millimeters.
Tolerances represent the allowable variation for a specific dimension.
For instance, if a CNC machining tool has a tolerance of ± 0.01 millimeters, it means that the tool
can deviate by 0.01 millimeters in each cut.
When provided with a drawing, Our CNC machining service can achieve CNC parts with tolerances
as tight as ± 0.0002 inches.
In the absence of a drawing, all CNC parts are manufactured according to our ISO 2768 medium
standard. We can also work to even tighter tolerances, such as ± 0.025 millimeters or ± 0.001
inches, when an engineering drawing specifies critical features.
CNC Turning Tolerances | ||
Limits for nominal size | Plastics | Metals |
0.5mm* to 3mm | ±0.1mm | ±0.05mm |
Over 3mm to 6mm | ±0.1mm | ±0.05mm |
Over 6mm to 30mm | ±0.2mm | ±0.10mm |
Over 30mm to 120mm | ±0.3mm | ±0.15mm |
Over 120mm to 400mm | ±0.5mm | ±0.20mm |
Over 400mm to 1000mm | ±0.8mm | ±0.30mm |
Over 1000mm to 2000mm | ±1.2mm | ±0.50mm |
Over 2000mm to 4000mm | ±2.0mm | |
*Please clearly indicate tolerances for nominal sizes below 0.5mm on your technical drawing. |
Applications of CNC Turning Parts
CNC machining is a highly utilized subtractive manufacturing process employed across a
multitude of industries.
It plays a crucial role in aerospace, automotive, aviation, transportation, and numerous other
integral sectors.
For instance, in the aerospace industry, the production of airplane components demands an
exceptional level of precision to ensure the seamless functionality of the entire aircraft.
Company Profile
FAQ's
1. What is the difference between rough turning and finish turning?
Rough turning and finish turning are two distinct phases in the CNC turning process, each serving
a specific purpose.
Rough turning is the initial stage where the primary objective is to efficiently remove as much
material as possible from the workpiece.
This process prioritizes material removal over precision and surface finish.
Its purpose is to rapidly shape the workpiece and bring it closer to the desired dimensions,
allowing for more efficient subsequent machining operations.
On the other hand, finish turning is the concluding phase of the turning process.
Here, the emphasis shifts towards achieving the desired level of smoothness and accuracy in the
final product.
Finish turning fine-tunes the workpiece's surface finish and dimensional accuracy, ensuring that
it meets the exact specifications and requirements.
In summary, rough turning focuses on material removal and shaping, while finish turning
concentrates on achieving the desired precision and surface quality.
2. Advantages of CNC Turning
CNC turning offers several advantages, making it a valuable machining process:
1. Versatility: CNC turning centers can be equipped with rotating cutters like end mills and drills,
expanding their capabilities to handle asymmetrical features and various machining tasks.
This versatility increases production efficiency and cost-effectiveness.
2. Speed and Efficiency: CNC turning enables faster production, reducing lead times and
increasing overall efficiency. The automation and precision of CNC systems contribute to
streamlined operations.
3. Radial Symmetry: Achieving radial symmetry in parts is relatively easy with CNC turning.
This capability simplifies the machining of cylindrical and symmetrical components.
4. High Precision: Mounting the workpiece in a chuck allows for high precision during CNC turning
operations. This results in accurate and consistent part dimensions.
5. Superior Surface Finish: CNC turning often produces a superior surface finish on workpieces,
enhancing their overall quality and appearance.
6. Safety: CNC turning offers a safer machining environment compared to manual operations,
as it minimizes the need for direct human involvement in the machining process.
In summary, CNC turning provides versatility, speed, precision, and superior surface finish,
making it a preferred choice for various machining needs.