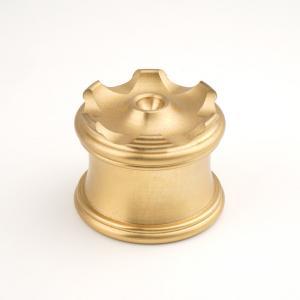
Add to Cart
Custom CNC Brass Processing High Demand CNC Aluminum Parts Machining
Milling Turning CNC Part Stainless Steel
Turning is a machining process where a cutting tool moves linearly while the workpiece
rotates. This term "turning" primarily refers to the generation of external surfaces through this
cutting action.
Conversely, when this essential cutting action is applied to internal surfaces like holes, it is
referred to as "boring."
Turning can be carried out manually using a lathe, often requiring continuous operator
supervision, or it can be automated with a lathe that operates independently.
The most common form of automation today is computer numerical control (CNC).
In the turning process, a workpiece made of a relatively rigid material, such as wood or metal,
is rotated while a cutting tool moves along one, two, or even three axes to create precise
diameters and depths.
Turning can be applied to the exterior of a cylinder to produce tubular components with various
geometries.
Components that undergo turning operations are commonly known as "turned parts" or
"machined components."
Product Details
Materials Suitable for CNC Turning
CNC lathe machining can produce high-quality parts with accuracy and precision in a variety
of raw materials. The CNC turning process can be applied to most hard materials and metals
such as:
Aluminum, Stainless Steel, Brass, Copper, Titanium, etc.
Common Materials | |
Name | Description |
Aluminum | High machinability and ductility, good strength-to-weight ratio. |
Stainless steel | High tensile strength, corrosion and temperature resistant. |
Mild steel | High machinability and weldability, high stiffness. |
Brass | Low friction, excellent electrical conductivity, golden appearance. |
Copper | Excellent thermal and electrical conductivity. |
Titanium | Excellent strength to weight ratio, used in aerospace, automotive and medical industries. |
POM | High stiffness, high accuracy, low friction, easy to machine. |
ABS | Common thermoplastic, impact resistant, easy to machine. |
Nylon | Excellent mechanical properties, thermal, chemical and abrasion resistant. |
CNC Turning Tolerances | ||
Limits for nominal size | Plastics | Metals |
0.5mm* to 3mm | ±0.1mm | ±0.05mm |
Over 3mm to 6mm | ±0.1mm | ±0.05mm |
Over 6mm to 30mm | ±0.2mm | ±0.10mm |
Over 30mm to 120mm | ±0.3mm | ±0.15mm |
Over 120mm to 400mm | ±0.5mm | ±0.20mm |
Over 400mm to 1000mm | ±0.8mm | ±0.30mm |
Over 1000mm to 2000mm | ±1.2mm | ±0.50mm |
Over 2000mm to 4000mm | ±2.0mm | |
*Please clearly indicate tolerances for nominal sizes below 0.5mm on your technical drawing. |
Applications of CNC Turning Parts
CNC turning parts is a popular choice for many products and components:
1. Sensor Parts 2. Auto Parts 3. Respirator Parts
4. Power Tools 5. Hydraulic Parts 6. Aircraft Parts
7. Dental Handpieces 8. Drone Parts 9. Motor Parts
10 .Bicycle Parts 11. Robotic Parts 12. Appliance Parts
Company Profile
FAQ's
1. How Do CNC Turning Machines Operate?
CNC turning machines operate through the following key steps:
1. Workpiece Setup: The workpiece, which can be any material or object to be machined,
is securely mounted onto the machine's chuck or collet. This setup allows the workpiece to rotate
during the machining process, ensuring stability and precision.
2. Tool Selection: Various cutting tools are chosen based on the specific machining tasks required.
These tools can include turning tools, grooving tools, threading tools, and drilling tools, among others.
3. CNC Programming: A computer-aided design (CAD) model of the component to be manufactured
is imported into a CNC program.
This program is then loaded into the CNC machine's computer, containing detailed instructions for
tool movements, spindle rotation speed, feed rates, and other essential parameters needed for the
machining process.
4. Machining Operations: The CNC machine executes the programmed instructions, with the spindle
rotating the workpiece while the cutting tools move along their designated axes.
This precise process gradually removes material from the workpiece, shaping it to achieve the
desired dimensions and features.
2. Advantages of CNC Turning
1. Quick Turnaround
Our state-of-the-art CNC machines enable us to produce highly accurate, fast-turnaround parts,
with some available in as little as 1 day.
2. Customized Finishes
You can choose from a diverse range of finishes for solid metal and plastic parts, all meticulously
crafted to meet your exact design specifications.
3. Material Variety
With an extensive selection of over 50 certified metal and plastic materials, CNC Machining offers
unparalleled material choices.
4. Precision
We maintain high-precision tolerances, typically within the range of +/-0.001″ to 0.005″, depending
on your specific requirements.
5. Scalability
CNC Machining is ideal for producing anywhere from 1 to 10,000 CNC machined parts, offering
scalability to suit your needs.