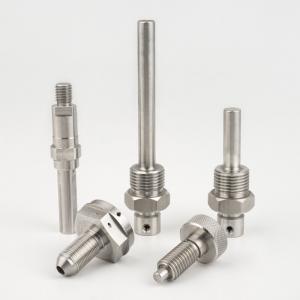
Add to Cart
Custom High Precision Stainless Steel Parts OEM Milling Turning Parts
CNC Machining Parts Aluminum Brass
CNC (Computer Numerical Control) machining is an automated process that involves using a
machine to remove material from raw stock based on computer-generated instructions.
It is applicable to a wide range of materials, from expanded polyurethane foam to nickel
superalloys. Common applications for CNC machining include manufacturing, crafting ornamental
furniture, and producing turbine blades.
The cost of CNC machining is influenced by factors such as precision requirements, surface finish,
quantity, material selection, and the complexity of the part being produced.
Product Details
CNC machining can be used for a wide variety of materials, with the most common being
aluminum, steel, brass, ABS, Delrin, and nylon.
But really, almost any hard material can be CNC machined.
Common Materials for CNC Machining | |
Material | Properties |
Aluminum | 2024: Good fatigue resistance and strength; excellent toughness at moderate to high strength levels; improved fracture toughness |
6061: Excellent machinability, low cost, and versatility | |
7075: High strength, hardness, low weight, and heat tolerance | |
Brass | Versatile and highly attractive copper/zinc alloy with warm yellow color accommodates severe forming/drawing |
Copper | High ductility and high electrical and thermal conductivity; develops attractive blue-green surface patina over time |
Stainless Steel | Excellent machinability and outstanding uniformity; good workability and weldability, high ductility and formability |
Steel Alloy | Mix of chromium, molybdenum, and manganese yields toughness, good torsional and fatigue strength |
Steel Mild Low Carbon | High machinability and weldability, high stiffness; good mechanical properties, machinability, and weldability at low cost |
Titanium | Excellent strength to weight ratio, used in aerospace, automotive, and medical industries |
ABS | Excellent impact resistance, good mechanical properties, susceptible to solvents |
Nylon | Excellent mechanical properties, high toughness, poor moisture resistance |
POM | High stiffness, excellent thermal & electrical properties, relatively brittle |
Post-processing and surface finishes for CNC machining
CNC-machined parts as they emerge from the machine often exhibit visible tool marks, a feature
that may not align with your specific part requirements.
Fortunately, there exists a multitude of post-processing techniques aimed at enhancing the surface
appearance and elevating attributes such as wear resistance, corrosion resistance, and chemical
resistance.
Methods like anodizing, bead blasting, and powder coating present viable options for refining the
final presentation of your custom parts, allowing you to achieve the desired surface quality and
performance characteristics.
Surface Finishing Options for CNC Machining | ||
Name | Applicable Materials | Can be Applied with |
Alodine | Aluminum | Media Blasting, Tumbling, Type II Anodizing* Type III Anodizing*, Type III Anodizing with PTFE* |
Anodizing | Aluminum | Media Blasting, Tumbling, Alodine* |
Black Oxide | Steel, Stainless Steel | Media Blasting, Tumbling, Passivation |
Electroless Nickel Plating | Aluminum, Steel, Stainless Steel | Media Blasting, Tumbling |
Electropolishing | Steel, Stainless Steel | — |
Hand Polishing | Acrylic | Enhanced cosmetic appearance |
Media Blasting | Aluminum, Steel, Stainless Steel, Brass, Bronze, Copper | All post processes except Electropolish and Powdercoat |
Nickel Plating | Aluminum, Steel, Stainless Steel | Media Blasting, Tumbling |
Passivation | Steel, Stainless Steel | Black Oxide, Electroless Nickel Plating, Zinc Plating, Tumbling, Media Blasting |
Powder Coating | Aluminum, Steel, Stainless Steel | — |
Tumbling | Aluminum, Steel, Stainless Steel, Brass, Bronze, Copper | All post processes except Electropolish and Powdercoat |
Vapor Polishing | CNC Polycarbonate (Clear, Black) | Enhanced cosmetic appearance, near optically clear applications |
Zinc Plating | Steel, Stainless Steel | Media Blasting, Tumbling, Passivation |
Applications of CNC Machining
CNC machining offers a wide range of applications across various industries.
Here are some examples:
1. Woodworking
CNC machining is commonly used in woodworking to create intricate and cost-effective wooden
furniture. It allows for the production of complex designs that would be time-consuming and
expensive when done manually.
2. Lettering and Engraving
CNC machines can perform precise engraving and lettering tasks, whether for artistic purposes
or marking serial numbers and patterns on parts.
3. Electrical Industry
The electrical industry relies on CNC machining for tasks such as drilling mounting holes in
printed circuit boards and crafting heat sinks from aluminum or copper for electronic components
that generate heat.
4. Pharmaceutical Industry
In the pharmaceutical sector, CNC machines are employed to manufacture precision equipment
used in pharmaceutical production. This includes metering pumps, ingredient-dispensing nozzles,
and packaging machinery.
5. Food and Beverage Industry
The fast-moving consumer goods industry benefits from custom material-handling machinery,
often incorporating CNC machined parts. Additionally, CNC machining is used to create molds
for injection-molded food packaging materials.
Company Profile
FAQ's
1. Advantages of the CNC Machining Process
CNC machining offers several advantages when compared to other manufacturing and machining
methods.
1. Enhanced Precision and Accuracy
CNC machines excel in producing identical components with consistent dimensions, ensuring
precision at a level that manual machining cannot match.
The computerized controls allow for unparalleled accuracy in manufacturing.
2. Expedited Turnaround Times
CNC machining can significantly reduce production lead times. Unlike traditional machines that
require manual setup for each operation, CNC equipment can make adjustments swiftly by
modifying the computer program.
Furthermore, these machines can operate continuously for extended periods without the need
for breaks, resulting in faster order fulfillment.
3. Scalability
CNC machining is ideal for both prototyping and large-scale production.
Thanks to its reliance on CAD files rather than intricate machine setup, prototypes can be swiftly
and accurately produced.
Once a part design is approved, it can seamlessly transition into full-scale production.
4. Versatility
CNC machining is versatile and adaptable, accommodating diverse designs in various materials,
including metals and polymers.
This flexibility makes it a suitable choice for manufacturing a wide array of components and products.
2. General Cost Reduction Strategies
Achieving cost reduction in manufacturing requires a thoughtful approach that considers various
factors. Here are some general tips to help reduce production costs:
1. Material Selection:
Choose popular materials and compare prices across different types.
Keep in mind that harder materials like steel and stainless steel tend to be more expensive than
softer materials such as aluminum or plastic.
2. Design Simplification:
Opt for 2D parts made from sheet material instead of 3D parts from block material.
Consider stacking 2D parts or using bending techniques to create 3D shapes.
Design parts to be multi-functional to reduce the number of distinct part types.
3. Volume Optimization:
Increase the quantity of parts to take advantage of economies of scale and reduce the cost per part.
4. Tolerance Management:
Use the loosest applicable tolerance to avoid unnecessary precision, which can increase production
costs.
5. Finish Selection:
Choose common and simple finishes to minimize costs.
Avoid multiple finishing processes whenever possible.
Consider using materials that do not require additional finishing steps.
6. Component Separation:
Convert single complex parts into multiple simpler components that can be assembled.
For example, when creating a large disk with a thin rod protruding from the center, design the disk
and rod separately rather than as a single piece.
This approach can reduce material waste and production costs.
7. Hole Tapping Optimization:
When tapping holes, avoid depths exceeding three times the hole diameter, especially when the hole
and bolt are of the same material.
Deeper holes often do not add significant strength but can substantially increase costs.
By implementing these cost-saving strategies, manufacturers can optimize their production processes
and reduce overall manufacturing expenses.