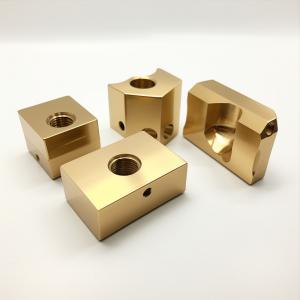
Add to Cart
Custom CNC Parts Cost Part CNC Machining Parts CNC Precision Milling Service
Our CNC machining services extend to the production of various parts, covering everything
from straightforward "as-machined" workholdings to complex geometric shapes.
Operating an extensive range of CNC mills and turning centers, our manufacturing facilities are
well-prepared to meet diverse requirements. Additionally, we have EDM and grinding capabilities
available upon request.
Offering precision with tolerances as precise as 0.05 mm (0.0020 in), we pride ourselves on
efficient lead times, providing delivery options within a short span of 1 business days.
Product Details
Brass is a metal alloy known for its low friction properties, exceptional electrical conductivity,
and distinctive golden appearance.
This material offers good machinability, making it suitable for a wide range of applications
that demand low friction and high electrical conductivity.
Common Brass Materials | |
No. | Properties |
Brass C3600 | It has superior machinability, thread rolling and knurling characteristics. Typically used in the manufacture of fluid connectors, threaded inserts, couplings, and more. |
Brass C3602 | It’s strength and resistance to corrosion with properties closely resembling that of steel. It is ideal for some of the most demanding conditions such as heavy industrial parts. |
Brass C3604 | It is used in the mass production of brass components. It is widely used in manufacturing hardware, connector, flange and other machine parts by lathe and CNC. |
Brass C4926 | A low leaded free cutting brass which conform RoHs and Reach environment regulations. Widely used on electronic parts, precision machine, valves, and related parts. |
Brass Finishing and Post-Processing
360 Brass has a shiny yellow finish that varies depending on surface roughness.
It can be hand-polished to increase its sheen, or media blasted for more of a matte texture.
Name | Machining Marks |
As machined | Visible, light surface scratches |
Smooth machining | Visible, light surface scratches |
Fine machining | Slightly visible |
Polishing | Removed on primary surfaces |
Bead blasting | Removed for non-cosmetic, removed on primary surfaces for cosmetic |
Brushing | Reduced for non-cosmetic, removed on primary surfaces for cosmetic |
Powder coating | Removed |
Black oxide | Visible |
Applications of CNC Parts
Various industries harness the capabilities of CNC machining to enhance efficiency and precision
in mass production. These industries include:
1. Aerospace:
CNC machinery is pivotal in the aerospace industry for the fabrication of intricate and precision
components used in aircraft and spacecraft.
2. Automotive Parts Manufacturing:
The automotive industry extensively relies on CNC machining for the production of precise and
customized components used in vehicles.
3. Medical Machine Manufacturing:
CNC machining plays a crucial role in the medical industry, contributing to the manufacturing of
intricate components for medical devices and equipment.
4. Transportation:
Industries involved in transportation, such as railways and mass transit, utilize CNC machinery for
the production of components ensuring efficient and reliable transportation.
5. Defense:
The defense industry benefits from CNC machining for the production of accurate and complex
components essential for various defense applications.
6. Marine:
In the marine industry, CNC machinery is employed for the manufacturing of precision parts used
in boats and marine equipment.
7. Oil and Gas:
The oil and gas industries leverage CNC machining to fabricate components used in exploration,
drilling, and extraction processes.
8. Electronics:
The electronics industry relies on CNC machinery for the production of intricate components used
in electronic devices, ensuring precision and reliability.
Company Profile
Factors Affecting Machining Costs
The cost of CNC machining projects is influenced by various factors that have a significant impact
on the overall cost calculation. Manufacturers looking to optimize their processes and manage
expenses effectively should have a thorough understanding of these key elements that determine
machining costs.
Let's delve into the factors that play a crucial role in determining the cost of CNC machining:
1. Material Selection:
The choice of raw material directly affects machining costs. Different materials come with varying
costs, availability, and machining characteristics. High-performance alloys, for instance, may be
more expensive than common metals. Material availability also affects pricing.
When calculating machining expenses, it's essential to consider the type of material required for
CNC machined parts and its associated cost.
2. Complexity of Design:
The complexity of the machined part or component is a significant cost determinant.
Parts with intricate features, tight tolerances, and complex geometries often necessitate advanced
machining techniques, specialized tooling, and longer machining time.
These factors increase overall costs due to the additional precision and expertise required to produce
such complex components.
3. Machining Time:
Machining time is a critical factor in CNC cost calculation. The longer it takes to machine a part,
the higher the cost. Machining time includes cycle time (the time spent cutting the part), setup
time (preparation and tool changes), and overall production efficiency.
Optimizing machining processes to reduce cycle time and enhance setup efficiency can minimize
costs and boost productivity.
4. Machine Tooling:
The choice and management of machine tooling have a significant impact on machining costs.
Considerations should include tooling costs, encompassing the purchase, maintenance, and
replacement of cutting tools.
The lifespan of cutting tools and the time required for tool changeovers affect production efficiency
and, consequently, cost. Proper selection, maintenance, and optimization of machine tooling can
help control expenses in CNC machining.
5. Volume and Batch Size:
Production volume and batch size directly influence machining costs. Economies of scale come into
play with larger volumes. The cost per part typically decreases as production quantities increase.
However, it's crucial to strike a balance between volume and setup time. Small batch sizes may have
higher costs per part due to increased setup time, while larger volumes benefit from reduced setup
time and lower costs per part.
6. Labor Costs:
Labor costs, encompassing the wages of CNC machining engineers and operators, make a
significant contribution to CNC machining expenses. Skilled operators with expertise in CNC
programming, setup, and operation are essential for efficient and accurate machining.
Labor-intensive operations or intricate part requirements may involve additional labor costs.
Finding the right balance between utilizing skilled labor and cost management is crucial in
controlling machining expenses.
7. Overhead Costs:
Overhead costs associated with CNC machining operations can impact the overall cost calculation.
These costs include facility expenses, utilities, administrative costs, quality control, and inspection.
Managing and optimizing these overhead expenses are vital for cost control and maintaining a
competitive edge in CNC machining.
8. Scrap and Rework:
Scrap and rework costs are important considerations in machining expenses. Material wastage due
to errors or deviations from specifications can significantly increase costs. Minimizing scrap through
effective quality control measures, precision machining techniques, and robust inspection processes
helps reduce material waste and the need for rework, ultimately lowering overall machining costs.
By comprehending and analyzing these factors that affect machining costs, manufacturers can identify
areas for improvement, implement cost-saving strategies, and optimize their CNC machining processes
to achieve greater efficiency and profitability.