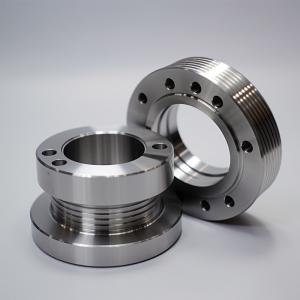
Add to Cart
CNC machining finds its best application in singular manufacturing projects and the efficient
production of a limited to medium quantity, spanning from several hundred to 1000 parts.
The economically sound choice for metal prototype fabrication is CNC machining.
Furthermore, when stringent tolerances are a prerequisite for your components, opting for
CNC machining becomes imperative.
Product Details
Stainless steel is highly resistant to corrosion and rust, making it suitable for situations
where a part may be exposed to the elements for a long period of time.
Stainless steel is also fairly malleable and ductile.
Common Stainless Steel Materials | |
No. | Properties |
Stainless steel 304/304L | The most common alloy and is known for its pristine surface finish. It has significantly higher corrosion and oxidation resistance. Typically used in the manufacture of sensor parts, shafts, machinery parts, medical parts, and more. |
Stainless steel 316/316L | It is slightly higher levels of chromium and nickel that exhibits improved heat tolerance, resistance to creep and pitting, and excellent tensile strength. Typically used in the manufacture of sensor, chemical & pharmaceutical equipment parts, and more. |
Stainless steel 303 | It is a non-magnetic, austenitic stainless steel with good resistance to mildly corrosive atmospheres, but significantly less than 304. Typically used in the manufacture of screw, gears, fittings, bushings, shaft, and more. |
Stainless steel 420 | It is a martensitic stainless steel with good corrosion resistance as well as strength and hardness. It is capable of being heat treated to a hardness of HRC 51 minimum. Typically used in the manufacture of pivots, cams, pump shafts, surgical instrument parts, valve components, and more. |
Stainless steel 440C | It is a martensitic stainless steel, and is the highest carbon content from 400 stainless steel series. It is usually heat treated to reach hardness of 58 - 60 HRC. Typically used in the manufacture of valve seats, piston, shaft, and more. |
Stainless steel 430 | It is a non-hardenable ferritic stainless steel with excellent finish quality. It has good corrosion resistance with good formability and ductility. Typically used in the manufacture of fittings, flanges fasteners, piston, and more. |
Stainless steel 430FR | It is a free-machining solenoid quality alloy, ideal for parts that require corrosion resistance and high electrical resistivity. It has excellent corrosion resistance in fresh water, gaseous, moderately acidic, and low chlorine environments. |
Stainless steel 630 | It is commonly referred to as 17-4 and is a precipitation-hardening martensitic stainless steel that offers superior corrosion resistance. It is magnetic, readily welded. Typically used in the manufacture of sensor housing, valve, pump shaft, and more. |
Stainless Steel Finishing and Post-Processing
We specialize in the production of custom-made products and offer surface treatment services
tailored to meet our customers' specific requirements and industry standards.
Our comprehensive solutions are both efficient and cost-effective, making us a one-stop
destination with the capacity and capability to provide integrated services.
Name | Can be Applied with |
Electropolishing | — |
Electroless nickel plating | Media Blasting, Tumbling |
Media Blasting | All post processes except Electropolish and Powdercoat |
Nickel Plating | Media Blasting, Tumbling |
Passivation | Black Oxide, Electroless Nickel Plating, Zinc Plating, Tumbling, Media Blasting |
Tumbling | All post processes except Electropolish and Powdercoat |
Zinc Plating | Media Blasting, Tumbling, Passivation |
Powder coating | — |
Black oxide | Media Blasting, Tumbling, Passivation |
Applications of Stainless Steel Parts
1. Medical:
Precision is paramount in the medical industry, and CNC machining is widely employed to
manufacture intricate components for medical devices and equipment.
2. Electronics:
The electronics industry benefits from CNC machining for the production of precise components
used in electronic devices, ensuring the functionality and reliability of the end products.
3. Defense:
The defense sector utilizes CNC machining for the production of accurate and durable components
used in military applications, ensuring the reliability and performance of defense systems.
4. General Manufacturing:
CNC machining is widely adopted in general manufacturing, contributing to the production of a
broad range of components used in various applications across industries.
CNC machining's versatility, precision, and efficiency make it a crucial manufacturing process in
these industries, contributing to the production of high-quality components essential for diverse
applications.
Company Profile
FAQ's
1. Can you ensure my designed component dimensions and tolerances are suitable
for production?
Count on our team of experienced professionals to provide valuable "Design for Engineering" (DFM)
support, evaluating the suitability of your designed component dimensions and tolerances for
production.
Understanding the need for prompt responses during the testing phase, we prioritize quick
turnaround times for quotes. Delve into our production process page for a detailed understanding
of the entire order progression.
2. What is your typical lead time? Can my parts be produced on a rush basis?
For screw machine products, our standard lead time, covering quoting, manufacturing,
and shipping, is typically one week. Our impressive on-time delivery rate surpasses 99%.
If you find yourself in need of a quicker turnaround, we are open to exploring expedited production
options, taking into account factors such as tooling, gauge availability, and material sourcing.
Don't hesitate to inquire!
3. Do you offer reverse engineering services or suggest cost saving measures?
Yes, we offer reverse engineering services, enabling us to extract design and engineering
information from various manufactured components. Additionally, our expertise extends to
assisting in the design process, recommending the best raw materials, and identifying efficient
machining protocols and finishing steps.
By considering the intended use of the part, we can often propose minor design adjustments,
material changes, or tolerance optimizations that contribute to cost savings while maintaining
the quality and performance of the part. Feel free to discuss your specific requirements with us!