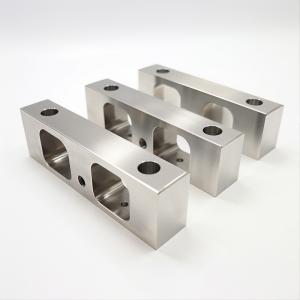
Add to Cart
CNC milling is the ideal method for producing intricate prismatic shapes and flat surfaces required
for a wide range of commercial and industrial applications. Our multi-axis metal CNC machines
offer unparalleled flexibility and precision without the need for fixed tooling.
Product Details
CNC machines are employed across a diverse range of materials, each having its optimal set of
machining parameters (speeds and feeds) for successful processing.
The most prevalent materials include:
1. Metal:
Metal stands out as the most frequently utilized material in CNC machining. CNC machines have
the capability to cut nearly any type of metal, from free-machining brass to high-performance
nickel superalloys like Inconel. Metal machining caters to various applications, ranging from injection
molds to the production of shafts and gears.
2. Plastic:
Although the majority of plastic parts are manufactured through injection molding, CNC machining
finds application in producing specific plastic components. Common materials include ABS
(acrylonitrile butadiene styrene), nylon, and polycarbonate. Plastic machining applications encompass
valve bodies, bushings, and the creation of injection molding prototypes to assess the overall
functionality before investing in costly molding tools.
3. Wood:
CNC routers are predominantly used for wood cutting and are generally more cost-effective than
standard metal-cutting CNC machines. Wood CNC machining is commonly employed for decorative
purposes, with applications such as furniture, window frames, and ornamental panels.
4. Foam:
Polyurethane foam, whether closed or open-cell, is frequently employed in CNC machining applications.
CNC routers can cut foam blocks to create secure packaging for high-value products.
An example is the use of foam in toolboxes to ensure the tools remain secure during transportation.
5. Composites:
CNC machines are regularly employed in processing composite parts. Composites may include
materials like aramid, fiberglass, or carbon fiber, which are highly abrasive to cutting tools.
Aerospace and marine composite components undergo machining for tasks such as adding fastener
holes and general trimming after the molding process.
Common Materials for CNC Machining | |
Material | Properties |
Aluminum | 2024: Good fatigue resistance and strength; excellent toughness at moderate to high strength levels; improved fracture toughness |
6061: Excellent machinability, low cost, and versatility | |
7075: High strength, hardness, low weight, and heat tolerance | |
Brass | Versatile and highly attractive copper/zinc alloy with warm yellow color accommodates severe forming/drawing |
Copper | High ductility and high electrical and thermal conductivity; develops attractive blue-green surface patina over time |
Stainless Steel | Excellent machinability and outstanding uniformity; good workability and weldability, high ductility and formability |
Steel Alloy | Mix of chromium, molybdenum, and manganese yields toughness, good torsional and fatigue strength |
Steel Mild Low Carbon | High machinability and weldability, high stiffness; good mechanical properties, machinability, and weldability at low cost |
Titanium | Excellent strength to weight ratio, used in aerospace, automotive, and medical industries |
ABS | Excellent impact resistance, good mechanical properties, susceptible to solvents |
Nylon | Excellent mechanical properties, high toughness, poor moisture resistance |
POM | High stiffness, excellent thermal & electrical properties, relatively brittle |
CNC Milling Tolerances | ||
Limits for nominal size | Plastics | Metals |
0.5mm* to 3mm | ±0.1mm | ±0.05mm |
Over 3mm to 6mm | ±0.1mm | ±0.05mm |
Over 6mm to 30mm | ±0.2mm | ±0.10mm |
Over 30mm to 120mm | ±0.3mm | ±0.15mm |
Over 120mm to 400mm | ±0.5mm | ±0.20mm |
Over 400mm to 1000mm | ±0.8mm | ±0.30mm |
Over 1000mm to 2000mm | ±1.2mm | ±0.50mm |
Over 2000mm to 4000mm | ±2.0mm | |
*Please clearly indicate tolerances for nominal sizes below 0.5mm on your technical drawing. |
CNC Machining Applications
1. Manufacturing:
CNC machining plays a pivotal role in general manufacturing, producing components with precision
and efficiency for various applications.
2. Medical Devices:
The medical industry leverages CNC machining to manufacture intricate components for medical
devices, ensuring precision and adherence to strict quality standards.
3. Robotics:
CNC machining contributes to the production of components for robotics, providing the precision
required for the functioning of robotic systems.
The adaptability of CNC machining makes it a valuable tool in the hands of machinists, enabling the
creation of diverse products across different industries, each with its unique material and
precision requirements.
Company Profile
How to Reduce CNC Machining Costs?
Reducing CNC machining costs necessitates a comprehensive approach that optimizes various
aspects of the manufacturing process. By implementing the following cost-saving strategies,
manufacturers can achieve greater efficiency and maximize their cost-optimization efforts:
1. Supplier Collaboration:
Collaborating with CNC machine suppliers is valuable for exploring cost-saving opportunities.
Engaging with suppliers to negotiate favorable pricing, especially for bulk material purchasing,
can result in cost reductions.
Manufacturers can also optimize supply chain logistics, improve delivery times, and reduce
transportation costs by establishing solid supplier relationships. Collaborative efforts can lead to
developing innovative solutions and cost-saving recommendations based on suppliers' expertise
and CNC machining industry knowledge.
2. Design Optimization:
Designing parts for manufacturability is crucial for cost reduction in CNC machining. Streamlining
the machining process and minimizing material waste can be achieved by simplifying the geometry,
minimizing tight tolerances, and reducing the number of operations.
Collaborating with design engineers to optimize part designs for CNC machining can significantly
reduce production time, tooling requirements, and overall costs.
3. Material Selection and Standardization:
Careful material selection and standardization can significantly save costs. Manufacturers can
reduce material expenses by choosing cost-effective materials that meet the required specifications.
Standardizing material options across product lines simplifies procurement, minimizes waste, and
enhances machining efficiency. Material availability, price, and compatibility with machining processes
should be considered during material selection.
4. Process Optimization:
Optimizing the machining process is essential for cost reduction. This involves evaluating and refining
various aspects of production, including toolpath optimization, minimizing setup time, improving
machine utilization, and implementing lean manufacturing principles.
Increasing productivity and lowering costs can be achieved by optimizing toolpaths to reduce
unnecessary movements and minimizing setup time through efficient work holding and tool change
strategies. Implementing lean manufacturing techniques such as 5S, value stream mapping, and
continuous improvement initiatives further contributes to cost optimization.
5. Automation and Robotics:
Integrating automation and robotics into CNC machining processes can significantly enhance efficiency,
reduce labor costs, and improve productivity. Automated systems can handle repetitive tasks,
allowing skilled operators to focus on more complex operations. Robotics facilitate precise and
consistent machining, resulting in higher-quality parts and reduced scrap.
By embracing automation and robotics, manufacturers can save costs through increased throughput,
reduced labor expenses, and improved process control.
By implementing these cost-saving strategies, manufacturers can effectively reduce CNC machining
expenses and enhance their competitive edge in the market. A comprehensive approach that combines
design optimization, material selection, process optimization, automation, and supplier collaboration
can result in significant cost savings while maintaining high-quality production.